弊社プラズマ処理の概要
ここでは、コロナ処理や、アーク等を用いた装置ではなく、
完全なるバルクプラズマを発生させた装置を主体に置き、説明しております。
種々の電極構造を用い、窒素ガス・希ガス等をベースに高周波電力を電極に印可し、プラズマを発生させることにより励起ガス(ラジカル)が生成され、ワーク表面に官能基や水酸基、アミン基、その他の親水基の付与や酸化反応により、濡れ性や、塗布性能、有機物除去等の処理が可能になります。添加ガスを変えることにより、選択的に付与される分子を生成し、撥水化、還元等、薄膜deposition、ドライエッチング等の処理が可能になります。また、洗浄工程や、メッキ処理前のプラズマ処理により、表面活性化し薬液の反応性を高め、洗浄性能の向上や、気泡の除去等に役立ます。それらの処理に関して、ワーク(被処理物)の性格や、次工程への状況を踏まえ、下記に纏めるプラズマ装置選定時の最適化のご参考になれば幸いです。また、接着材を用いない接着剤レス接着に関して、銅箔、基材間との分子結合を主体とし、エッジ効果を排除した接着が可能で、今後の5G、6G向けのFCCL等の製造に寄与できるものと考えます。
01purpose使用目的(大気圧プラズマ装置で可能な処理)
- 親水化(洗浄性能・塗布性能・気泡除去)
- 撥水化
- 表面還元
- 表面酸化
- 有機物除去(有機汚染・残渣物)
- 密着性向上(官能基/水酸基・アミン基の付与)
- 異種材接着(官能基/水酸基・アミン基の付与)
- 接着剤レス接着(分子吸着)
- 表面粗化
- 残渣物の無い常温乾燥
- 表面窒化
- 表面滅菌殺菌
- エッチング(有機表面・無機表面)
- 薄膜成長(Deposition)(SiO2・SiON・a-Si・etc)
- 無電解・電解メッキ前処理
- 離型性向上(精密金型)
- 粘着力制御
- 微粒,(有機無機)ナノ粒子への表面改質
02models大気圧プラズマ装置の処理形態を大きく分類すると3種に大別される
プラナー型
プラズマ発生電極部内(高電圧下)にワークが入るため、ワーク表面間でアークやストリーマやイオンアタックの発生頻度が高い。このため処理表面へのピンホールのダメージを生ずる。従って、金属や、金属薄膜、半導体等の導電物ワークは不向きであり、処理形態としては物理的及び化学的処理が混在するため、表面粗化処理に適しているといえる。欠点として処理後静電気が発生する。利点は高速処理ができる。
詳細を見るダウンストリーム型
プラズマ発生部とワークが隔離されており、励起ガス(活性種/ラジカル)のみの処理である為、ダメージもなく、完全ドライケミカル処理で分子結合を主体とした表面改質が可能。不織布やスポンジ状のワーク内部への処理も可能である。処理後の帯電も無く除電が可能。パーティクルフリー化も実現しクリーンプロセスに適している。
詳細を見るスポット型
局部への処理を目的とし、強い処理が可能である為、有機残渣物の除去に有効。多軸ロボットアームに装着すれば3D形状にも対応可能。処理ガスとして空気が使用できる。安価(200万円装置本体~)である。
詳細を見る03process width処理可能プラズマ処理幅(長さ)
- プラナー型
- 50mm~1500mm
- ダウンストリーム型
- 100mm~4500mm
- スポット型
- 5mm~30mm
04object被処理物とプラズマ形態
- プラナー型
- 絶縁物を主体とした有機表面、各種フィルム、シート状、ロール to ロール。粘着力制御、表面粗化。
- ダウンストリーム型・スポット型
- シート状、幅広平面への処理。無機表面、ガラス、金属表面、金属酸化膜表面、不織布状、繊維束状、グラスファイバー、各種フィルム、金型表面、半導体、ナノ粒子、3D形状液晶基板(ARRAY・CF・Cell)、タッチパネル基板、その他電子部品、光学レンズ(ガラス・プラスティック)
05original他社に無い弊社独自の装置特徴(ダウンストリーム型)
- 特殊電極構造によりプラズマ生成時のUV・DeepUV光量を従来比約1/80に減衰させたため、ワーク内部の分子間架橋特性変化やダメージ発生がない。
- 放電電極内でのイオン加速制御及びスパッタ効果の抑制効果から、Particle発生が無い(0.3μ以上及び2.83SLMのサンプリング時)。これにより、誘電体電極寿命が半永久的に使用でき、ランニングコスト低減になる。
- 窒素消費が少ない。(特殊電極構造により高密度ラジカルの発生が可能になり、弊社従来比率45%減少させることができる)
- 独自の電磁誘導等の高周波シールド性能と、高周波電力印可方法や波形の最適化により、半導体チップ上の処理も可能。(処理後のトランジスタ特性変化なし(4nm以上のL/S))
- 大気圧プラズマで生成されたラジカルは非常に短命である為、プラズマ発生エリアとワーク間距離を最小限にする構造(特許)により、高性能化が実現できた。
- 処理後のワークへの帯電はほぼゼロ。
- 微粒子等への高利率的な親水化処理。
06schema誘電体バリア(DBD)放電の内部模式図
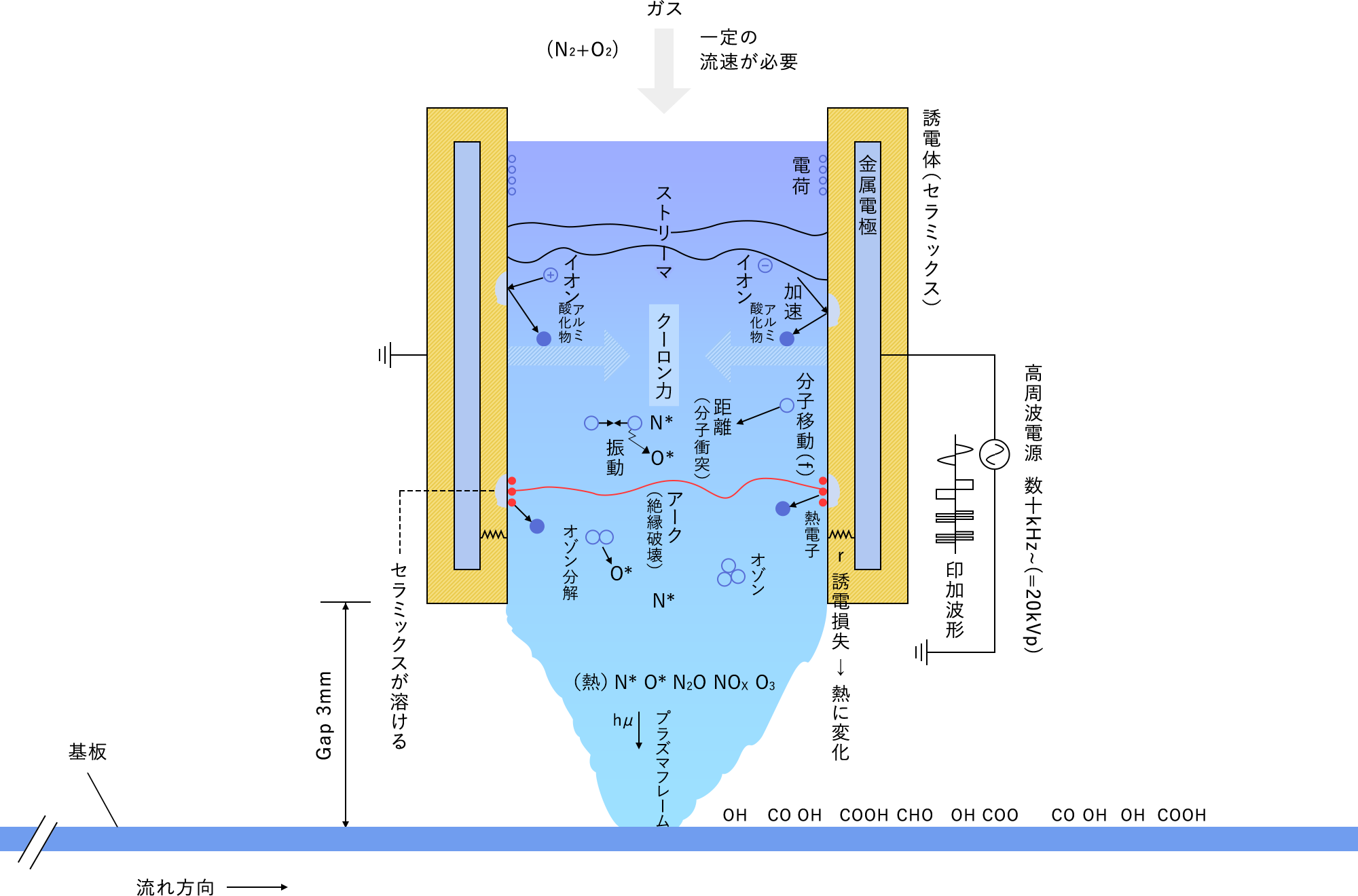